Smart Laboratory Management Platform System
1. Laboratory environmental safety and intelligent management system
1. Implementation specifications
"Civil Building Electrical Design Code" JGJ16-2008
"Intelligent Building Design Standard" GB50314-2015
"Communication Pipeline and Pipeline Engineering Design Standard" GB50373-2019
"Electrical Installation Installation Engineering Grounding Device Construction and Acceptance Code" GB50169-2016
"Technical Code for Security Engineering" GB50348-2018
"Civil Building Engineering Indoor Environmental Pollution Control Code" GB50325-2010 (2013 Edition)
"Technical Code for Energy Saving Monitoring System of Public Buildings" DBJ/T14-071-2016
"Technical Conditions for Data Transmission of User Metering Instruments" CJ/T188-2004
"Intelligent Building Engineering Construction Code" GB50606-2010
"Intelligent Building Engineering Quality Acceptance Code" GB50339-2013
"Building Electrical Engineering Construction Quality Acceptance Code" GB50303-2011
"Automation Instrument Engineering Construction and Acceptance Code" GB50093-2013
Code for Seismic Design of Mechanical and Electrical Engineering of Buildings GB50981-2014
General Safety Requirements for Information Technology Equipment GB4943.1-2011
Code for Fire Protection Design of Buildings GB50016-2014
Classification and Marking of Commonly Used Hazardous Chemicals GB13690-92
Classification and Product Name Numbering of Dangerous Goods GB6944-86
Regulations on the Safety Management of Hazardous Chemicals
2009 National Technical Measures for Design of Civil Building Engineering (Electrical Volume)
Other relevant national, industry and local current relevant specifications, regulations and standards
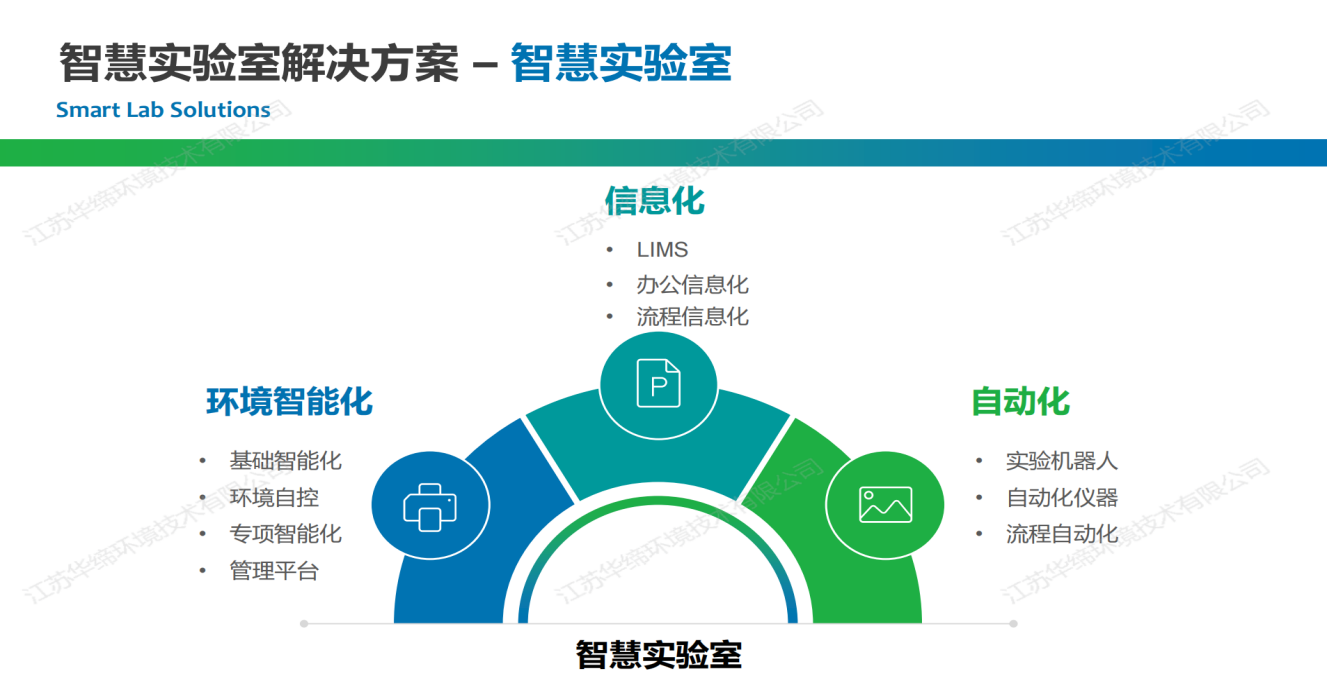
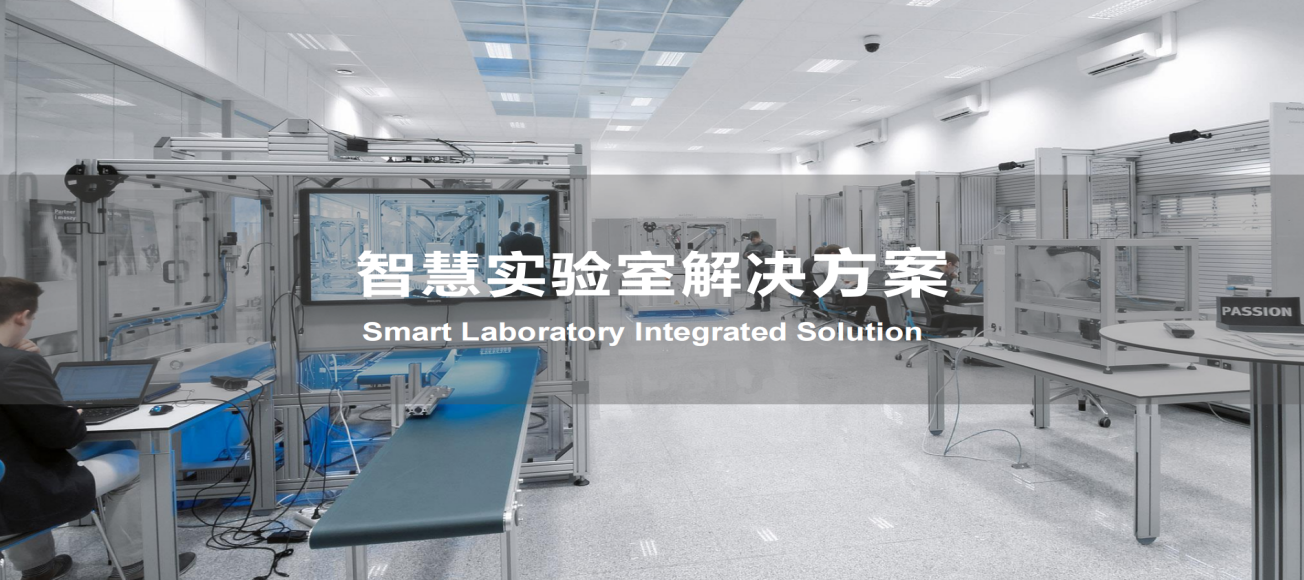
2. Laboratory Intelligent Central Control Management System Platform
1. System General Principles The
laboratory intelligent central control management system platform adopts digital twin technology, contains advanced laboratory digital construction models, Internet of Things and big data applications, and fully supports the digital transformation of high-end laboratories. The laboratory panoramic three-dimensional visualization monitoring system monitors environmental temperature, humidity, pressure, alarms, equipment and facilities in real time to ensure that laboratory data is fully three-dimensionally visualized, and realizes real-time human-computer interaction and data visualization decision-making assistance. Comprehensive management of laboratory environment space and professional application data, including laboratory user management interface configuration tool set, can realize global, regional, and equipment seamless docking visualization management, including data collection configuration development environment, physical operation environment, standard industrial protocol, and support for the Internet of Things MQTT protocol.
2. System requirements
2.1. ▲ The platform supports the Linux system and can be deployed on the Linux system. The Linux system can better protect the security of the system and inherit the characteristics of the Linux system itself;
2.2. ▲ The platform supports B/S browsing of data and can be developed in a pure B/S environment;
2.3. The platform is highly modularized and supports 3D interface display, data management, alarm management and other functions, which can be distributed or implemented in modules;
2.4. The platform supports HTML5 page technology and can browse data on mainstream mobile devices such as IOS and Android;
2.5. Laboratory smart central control management system platform management system integration requirements: adopt open mainstream commercial databases, and the background data automatic backup mechanism ensures the safe storage of all laboratory user data; strictly follow the international standard equipment and fault code system, establish a complete data storage standard, and provide the most solid technical foundation for future big data exchange and mining.
3. Laboratory digital model system
3.1. System requirements
Construct a 3D model of the laboratory, use 3D modeling software to build physical entities in a 3D scene, and use the 3D visualization digital twin platform to build a complex system with one-to-one correspondence, mutual mapping, and collaborative interaction between the physical world and the network virtual space. To meet the needs of laboratory construction, it includes the following functions:
1) Virtual feedback: Through the platform's powerful 3D engine, 3D simulation of facilities and equipment is realized, and real-time equipment data is obtained based on the digital twin models of buildings and facilities.
2) 3D display: Build a 3D visualization data twin platform for smart laboratories, combine building information models, IoT perception systems, and video surveillance systems to achieve time + space integrated presentation of real-time monitoring data, and realize real-time dynamic monitoring perception, event linkage, and command and dispatch applications.
3.2. Work content
1) Laboratory environment simulation model
Establish a 3D model, including the building facade, experimental area, roof and other areas,
including the following professional systems: laboratory room environment monitoring system, laboratory air supply and exhaust system, laboratory access control system, laboratory video surveillance, laboratory gas supply system, laboratory pure water system.
4. System requirements
4.1. It should be reliable and real-time, and adopt a mature and advanced platform; it can adopt multi-task industrial standard technology to ensure its openness and scalability; the architecture should meet the requirements of standardization and normalization; it should widely adopt distributed processing technology and redundancy technology, and have good portability, scalability and networking functions; it should be convenient for the expansion and upgrading of functions and systems, and fully guarantee the investment benefits of the laboratory, so that the system can adapt to the increase of functions and the expansion requirements of scale.
4.2. It should be ensured that the failure of the monitoring host does not affect the independent completion of the monitoring function of the controller. When the external power supply of the controller is cut off, its related status data can also be sent to the monitoring host. Once the power is restored, all the equipment affected by the power outage can also be automatically reset without resetting.
4.3.▲The platform is based on the WebGL standard and the threejs framework, and supports the rapid construction of a web-based model browsing application;
4.4.▲The platform supports the import of model files in glb and gltf formats;
4.5.▲The platform supports vectorized real-time 3D visualization functions, and can view the laboratory 3D scene by rotating, zooming in, zooming out, moving, etc. It supports 3D perspective roaming, 3D perspective positioning, dynamic association of 3D scenes and data, and other functions to achieve full and convenient information monitoring of the laboratory;
4.6. The platform has a multi-application integration architecture. In addition to process data, it supports video, geographic information, management data, and IT/Web information integration;
4.7. It supports HTML5 page technology, and can browse data on mainstream mobile devices such as IOS and Andoid, and can display the screen on the mobile phone or PAD.
4.8. The platform supports docking with business systems, can reshape the data structure of business systems and business management processes, and supports form applications, including: form collection, processing, and statistical applications;
4.9. The platform has more than 100 built-in components, supports ecahrt and various component special effects, and can flexibly and quickly customize various interactive large-screen visualizations. The platform provides business large-screen visualization templates;
4.10. Support users to add basic components to the page by dragging and dropping. The tool is pre-set with a web component library (including layout, navigation menu, breadcrumbs, labels, progress bars, message prompts, warnings, input, folding panels, cards, picture carousels and other category components) and a large-screen component library (including line charts, bar charts, pie charts, radar charts, scatter plots, word cloud charts, marquees, dashboards, videos, multi-line lists, China maps and other category components) to perform free layout design and minimize the user's development workload;
4.11. Support users to add 3D components to the page by dragging and dropping to build 3D outdoor or indoor scenes. The tool pre-set 3D component library contains more than 5 categories of components.
4.12. Support users to customize the styles of each component, such as component color, size, text, legend, etc., and different components contain different configuration items;
4.13. Support users to quickly generate form entry pages by configuring fields through the tool designer;
4.14. The platform has a rich component library and various types of B-side application templates;
4.15. Interface-based data integration is realized to achieve access, aggregation and centralized management of multi-source heterogeneous data. Support link adaptation of mainstream data formats such as Oracle, MySQL, Socket, Webservice, Kafka, MQTT, etc.;
4.16. Support users to manage applications, multiple applications are laid out in a card-like manner and basic information is displayed, and support creating, deleting, and searching for applications; 4.17. Support
users to preview the complete application or a single page, generate temporary sharing links or publish.
4.18. Adopting the front-end and back-end separation technology, the front-end system administrator has the monitoring authority of the system, and the back-end system administrator has the configuration authority of the system. The front-end and back-end authority are managed in a partitioned manner to avoid system crashes caused by misoperation and to ensure the stability of the system to the greatest extent.
4.19. It contains a user management interface configuration tool set, which can realize global, regional and equipment seamless docking visual management;
4.20. It is built on a high-speed local area network LAN and adopts the internationally accepted open network transmission protocol TCP/IP, so that various systems can share and integrate information on the same network.
4.21. The main information of each system can be exchanged and linked.
4.22. It has multi-dimensional alarm management capabilities.
4.23. Achieve continuous and uninterrupted operation to ensure the normal operation of the system 24 hours a day, 365 days a year.
4.24. With 3D chart display and analysis of real-time and historical data, adopt enterprise-level data acquisition system, support data storage in different database systems, and perform trend and chart analysis of real-time and historical data.
4.25. Adopt distributed alarm management system to view real-time alarm information.
4.26. Support real-time data display and historical data playback;
4.27. The software includes at least the following aspects
1) Rich data interfaces, which can access any equipment or system with standard protocols;
2) The platform adopts microservice architecture, fully supports the Internet of Things architecture, supports http protocol, supports mobile and cross-platform applications, etc.;
3) The platform can carry out multi-person collaborative operation development and quickly complete engineering development and deployment
4) The platform supports local snapshots, off-site disaster recovery, and multi-site backup functions;
5. Alarm service requirements
5.1. It can integrate multi-professional and multi-dimensional security alarm data such as building mechanical and electrical professional alarm data and controlled product use management alarm data.
5.2. Support classification and grading of alarm data, and push and real-time reminders to different responsible persons or groups of responsible persons according to type, level and alarm object.
5.3. The system needs to provide multiple alarm information management dimensions including (but not limited to) grading, grouping, department, region, and profession, so as to realize the responsibility of safety alarm management.
5.4. Alarm recipient screening conditions can be set, and management responsible persons can be configured by department and region. Filter conditions can be set according to the alarm content and pushed to the designated recipient.
5.5. Comprehensive management of laboratory alarm information, alarm thresholds and triggering rules can be set, and trigger alarms can be viewed in real time.
5.6. Alarm for abnormalities during equipment operation and use. Multi-level alarm value ranges, alarm grouping and grading, notification rules and notification upgrades, real-time query and historical analysis statistics, alarm processing and recovery life cycle management, etc. can be configured.
5.7. The alarm level is not less than 4 levels, divided according to the severity, and pushed to the relevant person in charge defined by the laboratory user. 5.8. Alarm
notification methods include: email and mobile phone text messages, and the recipient group and notification method can be customized as needed.
3. Laboratory Environment Safety and Smart Management Special Application System
1. Laboratory Instrument Monitoring & Management System
1.1. System General Principles
The laboratory instrument monitoring & management system should be centered on scientific research, supported by automation and open management, improve infrastructure, unify software and hardware platforms, standardize work processes, and implement hierarchical authorization management. It should establish an information management platform covering safety and security, scientific research resources, and work processes, and realize automatic, advanced digital, information-based, and open intelligent management.
1.2. Software Requirements
1) Overview: It can display the statistical data of the instruments managed by the system, the instrument usage statistics chart, etc.
2) Instruments: It can display the basic information, usage information, and reservation information of the instruments managed by the system.
3) Control device settings: It can set the instrument's control device parameters, power information parameters, etc., and view the instrument's real-time power consumption data.
4) Instrument manager settings: It can set the instrument's management personnel, and the management personnel can approve the instrument's reservation.
5) Usage authority management: It can set the instrument and personnel's usage authority matching. Personnel with usage authority can use the instrument in real time or can reserve the instrument online.
6) Usage record query: It can view the instrument's usage record, filter it according to needs, and export the form for archiving.
7) Card swipe record query: You can view the card swipe record of the instrument, including the card swipe record without permission.
8) Appointment list: You can view the instrument appointment status and appointment information.
9) The system can automatically identify and authorize instrument users through card swiping and other methods. Effectively divide the security responsibilities of instrument users, grant different levels of authorization, and achieve online and offline closed-loop management.
10) The system should support online appointment and appointment review functions to ensure the openness of specific instruments.
11) It can collect usage process data, such as user information, usage time, electricity consumption data, etc.; it can connect to the data integration platform to provide unified management methods.
12) The system can collect and form laboratory user usage records, which can be exported. The records include: instrument name, instrument number, instrument department, user, user department, start time, end time, usage time, and remarks.
13) ▲The system should have a unified login interface and unified laboratory user account information with the laboratory smart central control management system platform.
14) ▲The system should share the database with the laboratory smart central control management system platform, and uniformly manage data to ensure data security.
15) ▲The system should be centrally managed by the laboratory intelligent central control management system platform.
16) ▲The alarms generated by the system should be centrally managed and pushed by the laboratory intelligent central control management system platform.
17) ▲The equipment involved in the system shall be centrally managed by the facility management of the laboratory intelligent central control management system platform.
1.3. Software Function Requirements
1) Instrument information management: The system administrator can manage the basic information of the instrument, including the modification of basic information such as the addition, deletion, and query of the instrument. The basic information of the instrument includes the instrument name, category, department to which the instrument belongs, instrument person in charge, placement location, etc.
2) Instrument supervision and monitoring management
3) Instrument working status: including whether the instrument is turned on, standby, working, operator, usage time, etc. The administrator can remotely grasp the instrument working status, including idle status, usage status, user, usage time, etc.;
4) Instrument working data: The system can collect real-time power consumption data of the instrument, including the instrument's working voltage, working current, power consumption, etc. The data can be uploaded to the central control system for statistics.
5) On-site management of instrument use: The use of the instrument can be managed on-site through the instrument use manager, instrument energy consumption monitor, and instrument monitoring management system. Including authority management of instrument use and reminders such as timeout. System reminders include buzzer, LCD display, etc.
6) Abnormal alarm: When abnormal use of equipment occurs, including unauthorized personnel swiping cards to attempt to use, abnormal power failure, unauthorized opening and use, etc., the system alarm will be triggered, and the alarm information can be queried in the background of the server.
7) Experimental data summary and analysis: The system can summarize all instrument usage information and analyze it, such as analyzing the usage rate of a single device, the usage frequency of each device in the laboratory, work efficiency, etc. The specific analysis needs can be customized according to the customer.
8) Instrument use reservation
9) The system supports online reservation function. Users can make reservations for the corresponding instruments online. The instrument can be used on time only after the instrument administrator has reviewed and approved it;
10) The system can set reservation rules, such as open reservation time period, single reservation cycle and advance reservation threshold, etc.
2. Laboratory controlled product management system
2.1. System general provisions
The laboratory controlled product management system forms a complete controlled product collection information database by realizing the automated management of controlled product collection and return, realizes the informatization of controlled product management, and strictly controls the collection of controlled products.
The safety management of laboratory controlled materials runs through the whole process of use management. The comprehensive supervision and management of controlled materials mainly involves the safety monitoring and management of controlled materials through the monitoring means of electronic computer networks, and the controlled materials are stored separately according to different types of stored controlled materials.
2.2. Technical standards
1) "Code for Fire Protection Design of Buildings" GB50016-2014
2) "Classification and Marking of Commonly Used Hazardous Chemicals" GB13690-92
3) "Regulations on the Safety Management of Hazardous Chemicals"
4) "Classification and Name Numbering of Dangerous Goods" GB6944-86
2.3. Software requirements
1) The various information of controlled materials can be automatically identified through electronic tags.
2) It can meet the management requirements of application, storage, retrieval, weighing, movement, positioning, etc. of controlled materials with different characteristics, and form different management processes.
3) The storage environment of controlled materials can be monitored, such as storage temperature and humidity, concentration of harmful gases, etc.
4) It can carry out information management of controlled materials, including electronic information of various products and standard information database, which is convenient for querying inventory, characteristics, shelf life, usage regulations and purchase information.
5) It can collect usage process data, such as storage environment data, access data, personnel entry and exit data, inventory data and positioning data; it can connect to the data integration platform to provide unified management means; it can form access record forms, which can be exported, and the content includes: the type of controlled items accessed, the access person, the access time, the access quantity, the manager and the inventory balance after access, etc.
6) It can monitor usage behavior through various means, such as environmental monitoring, video monitoring, real-time capture and electronic sensing, to prevent accidents and human omissions, and achieve pre-prevention, in-process alarm and post-event traceability.
7) It can effectively divide the safety responsibilities of the controlled product users, give different levels of authorization, improve the controlled product usage process and risk control measures, and achieve online and offline closed-loop management.
8) The system should be linked with the laboratory intelligent central control management system platform, and the multi-terminal display interface should display the real-time environmental information and inventory records of the controlled product warehouse and the controlled product intelligent management cabinet; the location of the collected controlled products should be displayed on the multi-terminal display interface.
9) The controlled goods warehouse intelligent management station and the controlled goods intelligent management cabinet must be equipped with independent clients and realize the following functions:
Client of controlled goods intelligent management cabinet
Automatic identification of deposit and withdrawal: can automatically identify the items in the deposit and withdrawal cabinet and upload the records;
Storage environment collection: can automatically collect and upload the environmental parameters in the display cabinet;
Illegal operation alarm: when abnormal temperature and humidity, illegal door opening, door opening timeout and other abnormalities occur, an alarm is generated and uploaded;
Function expansion: ▲It can realize the unified database with the laboratory intelligent central control management system platform to realize cross-system function expansion application.
Client of controlled goods warehouse intelligent management station
Automatic settlement identification: can automatically identify the items placed on the table, and can store them in the warehouse area or take them out of the warehouse area;
Environmental collection: can automatically collect and upload the environmental parameters of the warehouse area;
Inventory query: can query the inventory of the warehouse area and the inventory of the controlled goods intelligent management cabinet in the warehouse area;
Warehouse area management: can set the relevant management parameters of the warehouse area;
Function expansion: ▲It can realize the unified database with the laboratory intelligent central control management system platform to realize cross-system function expansion application.
2.4. Software Function Requirements
1) Overview: It can display the real-time environmental data of the controlled goods warehouse and the controlled goods intelligent management cabinet, and the statistical data chart of the use and storage of controlled goods.
2) Controlled goods management: It can establish a controlled goods management directory, set the classification of controlled goods, manage the control method of controlled goods, and enter the basic information of controlled goods.
3) Warehouse and cabinet management: It can manage the parameter information of the controlled goods warehouse and the controlled goods intelligent management cabinet.
4) Inventory management: It can view the inventory in the controlled goods warehouse and the controlled goods intelligent management cabinet, which can be viewed by location or by controlled goods.
5) Access management: It can view the access records of controlled goods, filter them as needed, and export the form for archiving.
6) Authorization management: It can manage the personnel permissions of entering and exiting the controlled goods warehouse and opening the controlled goods intelligent management cabinet. 7)
Log query: It can view all records of system use, including operation logs and exception logs.
8) Settings: It can define the "source", "destination" and "purpose" fields for the warehouse management station to access controlled goods.
9) Automatic identification of controlled goods
The system can automatically collect data such as the type, status data, and weighing quality of controlled goods, and can automatically enter the system;
settlement within the warehouse area: the collection and storage operations of controlled goods in the warehouse area can be automatically identified and the information can be automatically stored;
automatic identification of controlled goods intelligent management cabinets: controlled goods can be automatically identified and recorded when they are stored in and taken out of controlled goods intelligent management cabinets.
10) Standardization of operating procedures
The system can standardize the operating procedures such as the application, storage, access, and transfer of controlled goods through system instructions to operators, reduce dependence on personnel experience, and improve efficiency. The controlled items can be identified and tracked to achieve full automation management; the track
of the collection and use of controlled items can be queried (except for non-customized tracks);
the process of claiming and accessing: different processes are set up for different types of controlled items, including ordinary items that can be directly collected and stored, controlled items that need to be weighed when collected and returned, and strictly controlled items that are only weighed in the warehouse;
alarm system: different alarm forms can be set for controlled items with different management processes (on-site sound and light alarm, platform push alarm), and the illegal exit of controlled items in the warehouse and the unclosed doors of the controlled items intelligent management cabinet will be reported on site and in the background.
11) Intelligent storage environment monitoring
The system can record temperature, humidity, and gas concentration data, provide abnormal alarm information, including leakage concentration detection and temperature and humidity abnormal analysis, and automatically transmit sensor information to the platform;
environmental data in the warehouse area and the intelligent management cabinet of controlled items: the temperature, humidity, gas concentration and other data in the warehouse area and the intelligent management cabinet of controlled items can be collected through special sensors;
data display and storage: all environmental data can be displayed locally and on the platform, and recorded and stored.
12) Informationization of controlled product storage
Controlled product statistics include controlled product attribute information, system attribute information, related personnel information, etc. All kinds of statistical information tables can be exported through the database, combined with various reports to build a complete controlled product traceability system;
Label information: The system can enter controlled product information, including the category, name, level, specification, unit, control method, etc. of controlled products. In the background management system, you can create, edit, delete controlled product information and bind labels. This information can be automatically synchronized to the local management system;
Inventory information: The background and local management system can query and manage the storage location, type and quantity of controlled products;
Operation log: The operation log can record the operation time, operator name, operation content, abnormal situation, etc., and can be selected and queried by operator, time, operation type, etc.
13) Clarification of usage rights
The laboratory controlled product management system divides personnel into three levels of authority: administrator, approval personnel, and user personnel, mainly in the warehouse area, controlled product entry and exit operations, data query, surveillance video record query, management operation, etc. Superiors can authorize subordinates to operate in different aspects.
14) Unmanned on-duty
The system can record the flow of controlled items by itself and can judge abnormal situations. Its video camera system can work normally without access to the Internet and can record at least 30 days continuously and 7*24 hours all-weather video. No personnel are required to be on duty on site, and any problems can be traced by retrieving the video recordings of the corresponding period.
2.5. Management requirements of controlled items intelligent management cabinet
1) Functional requirements of the management system of controlled items intelligent management cabinet: The controlled items intelligent management cabinet uses the cabinet as the main carrier, which can be used in series or individually, and can also be placed in the regional management system. Each single cabinet can achieve the function of managing controlled items separately.
2) Operation management requirements of controlled items intelligent management cabinet: The controlled items intelligent management cabinet body needs to be installed with an identity recognition system. Laboratory users need to swipe their cards to open the cabinet door. Unauthorized laboratory users cannot open the door. The operations between opening the door and closing the cabinet door are considered to be the operations of the door opener, and the system will record the information.
3) Requirements for storing and retrieving controlled items in the intelligent management cabinet for controlled items: Laboratory users can take out or deposit controlled items after opening the cabinet door. Taking out controlled items is regarded as a collection operation for controlled items, and depositing controlled items is regarded as a replenishment operation for controlled items. These operations must be recorded in the system.
4) Management requirements for illegal operations: Laboratory users may make mistakes when performing controlled item operations in the intelligent management cabinet for controlled items, such as depositing controlled items with unrecognizable labels, taking out controlled items that are not within their authority, or even forgetting to close the door and other unexpected situations. For these illegal behaviors, the intelligent management cabinet for controlled items must issue a buzzer alarm to remind the operator and record them in the system at the same time to find the causes of related events that occurred.
5) The intelligent management cabinet for controlled items is equipped with a special Venturi exhaust valve (DN100)
Valve specifications: DN100;
using a corrosion-resistant Venturi valve specially designed for HVAC control;
mechanical automatic device, no external power required;
When the pressure difference before and after the valve is between 150Pa and 750Pa, the pressure is irrelevant;
air volume control accuracy: ±5% of the controlled air volume;
working temperature: 0 to 50℃;
3. Laboratory temperature and humidity monitoring system
3.1. System requirements
1) ▲The system should have a unified login interface and unified laboratory user account information with the laboratory intelligent central control management system platform.
2) ▲The system should share the database with the laboratory intelligent central control management system platform, and uniformly manage data to ensure data security.
3) ▲The system should be uniformly managed by the laboratory intelligent central control management system platform for authority management.
4) ▲The alarms generated by the system should be uniformly managed and pushed by the laboratory intelligent central control management system platform.
5) ▲The equipment involved in the system is uniformly managed by the facility management and asset management of the laboratory intelligent central control management system platform.
3.2. Software function requirements
1) Support various monitoring indicators such as high temperature, normal temperature, low temperature, ultra-low temperature, relative humidity, etc., to achieve full monitoring of unattended experimental processes, storage processes, and culture processes.
2) It does not rely on any experimental equipment and manufacturers, and the recorded data is objective and fair, in compliance with FDA21CFR part11 specifications.
3) Make full use of the Ethernet network, without the need to lay out special complex lines. The number of monitoring points is unlimited.
4) All test data are automatically recorded 24 hours a day, 7 days a week, reducing manual workload and human errors. The standardized electronic data format makes data records more accurate, complete, standardized and traceable.
The system supports real-time monitoring, real-time recording and real-time alarm. Data is updated synchronously, 24 hours a day, 7 days a week, and risk warnings are issued within 1 second at the fastest. The system can connect to the platform to push alarm information.